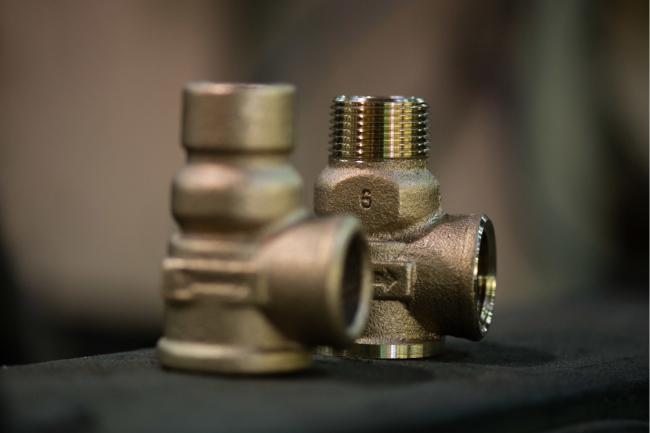
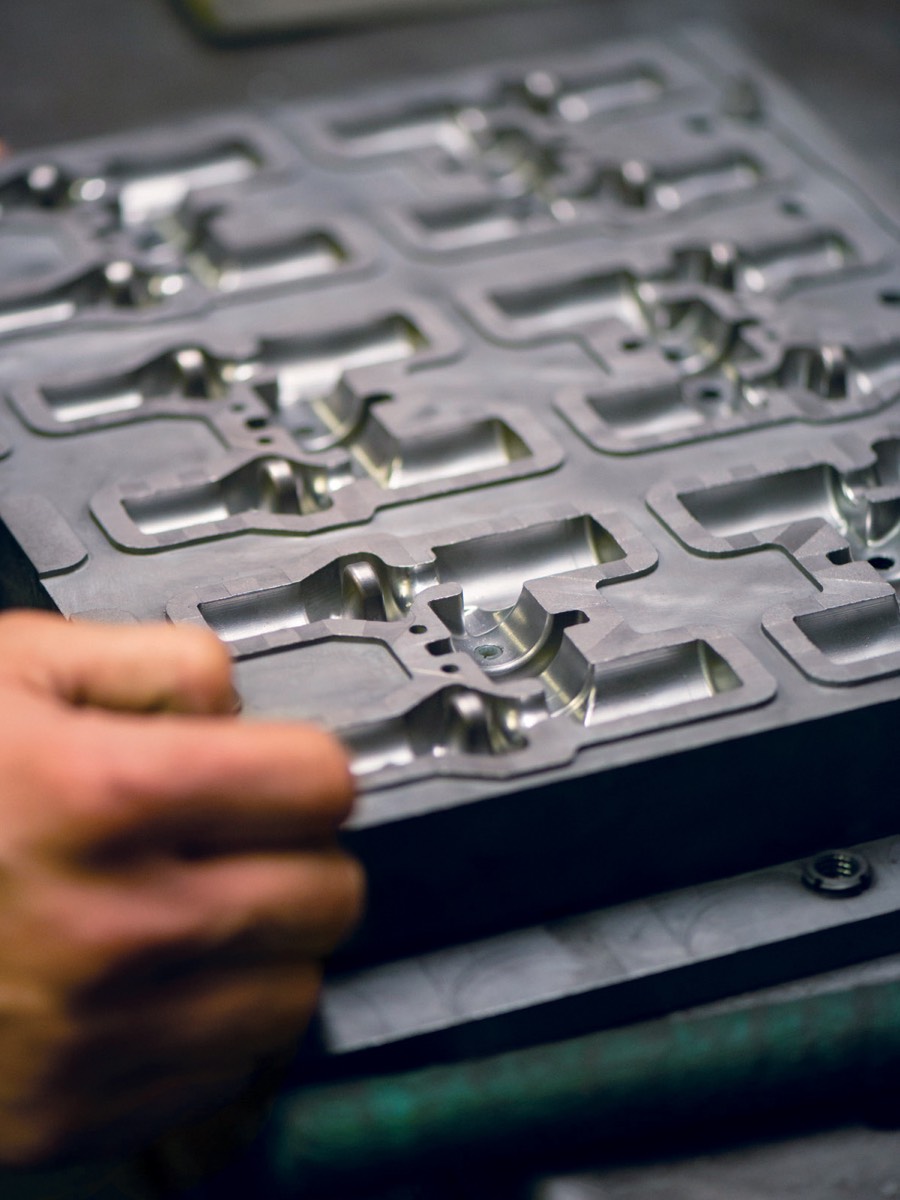
Partnerships are the core of our business
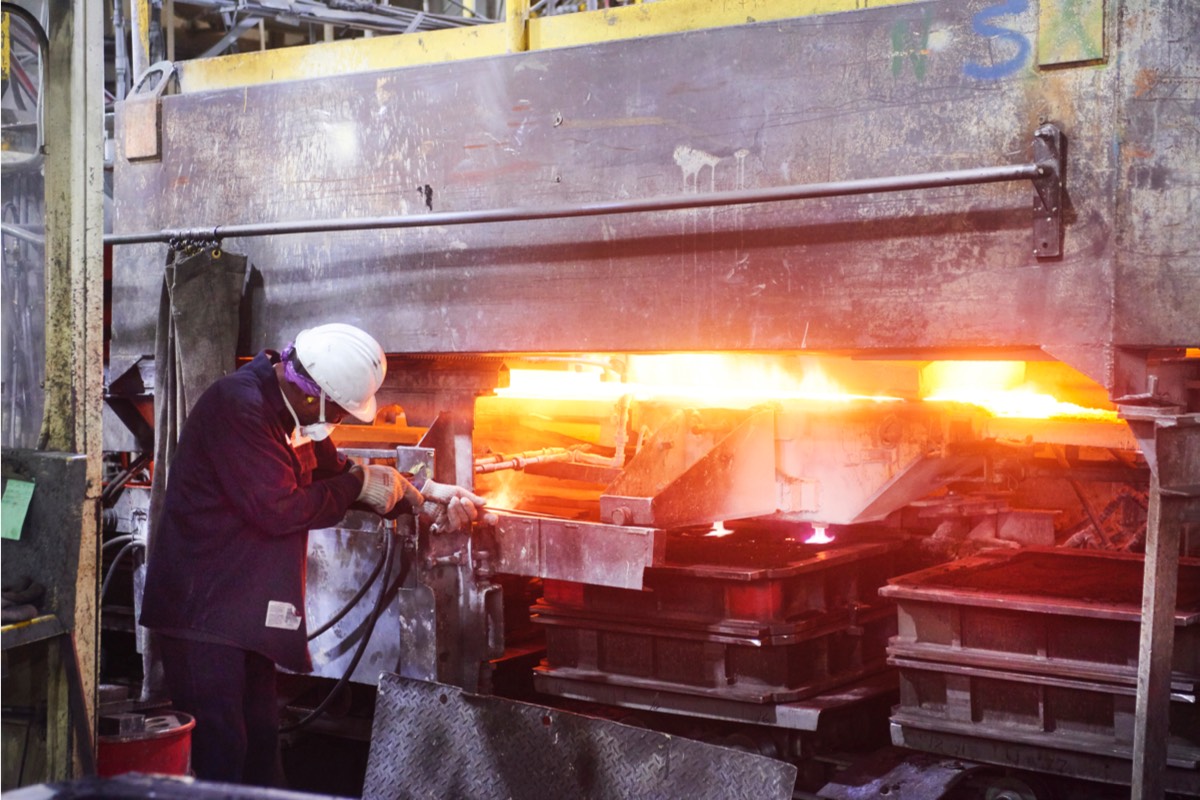
Sloan Foundry has been committed to creating strong long-term partnerships by providing high quality, engineered, state-of-the-art, copper-based castings and machined parts for OEM companies around the world for over 40 years.
Our mutually beneficial arrangement allows you to create alloy components without the need to invest in expensive new facilities, equipment, technology or staff.
Working with Sloan Foundry can help your business reduce costs, increase turnaround times and scale up your manufacturing capacity. Made in the USA means shorter lead times. Sloan Foundry customers receive shipments within 4 days as compared to up to 90 days from overseas foundries.
At Sloan, our foundry is your foundry.
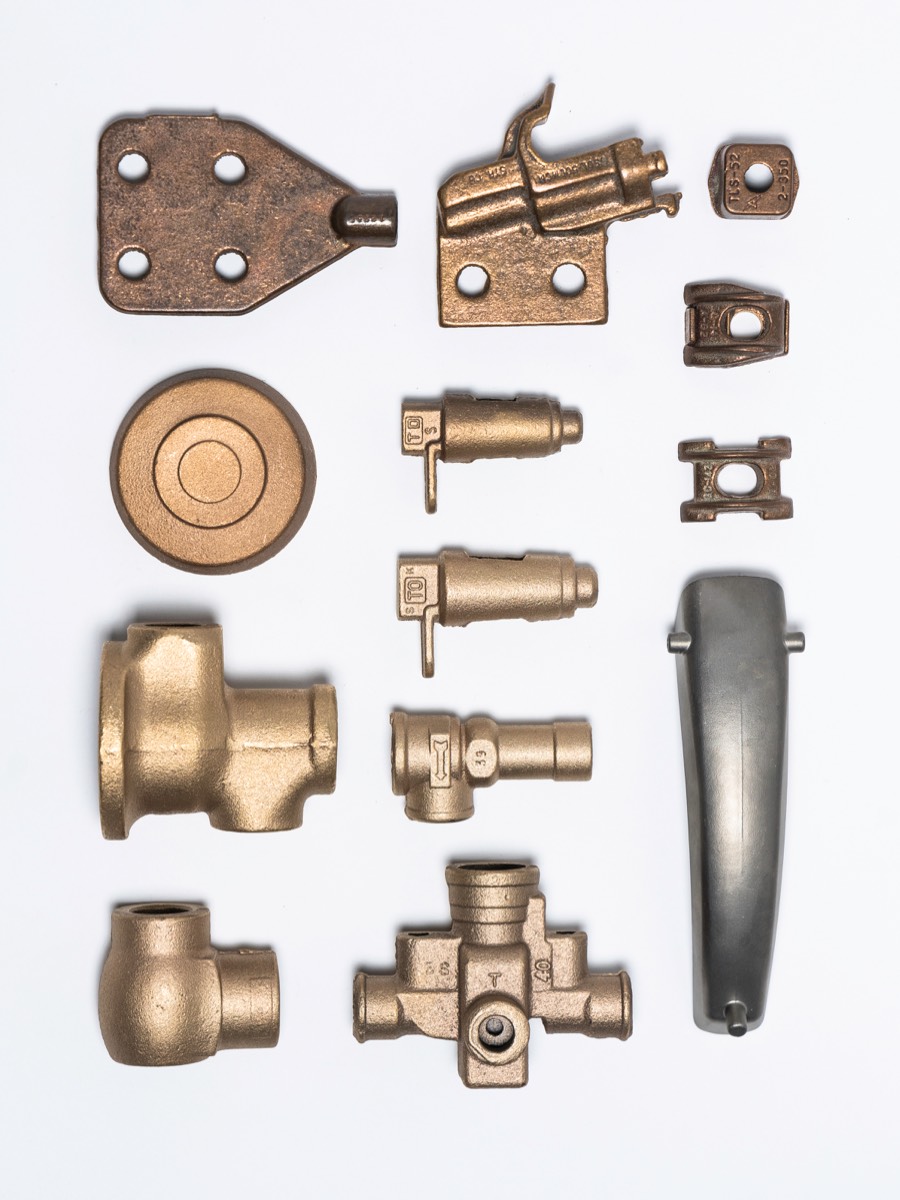
Products for every market
No single market dominates our portfolio. We have spent decades establishing relationships with a diverse array of companies in various verticals, and are always looking to expand our partnerships.
Plumbing
Time and pressure water valves, valves, flushometers, faucets, stops, pumps, impellers, cooling and heating fittings, water meters, hydrants, valve seats, pipe fittings, water heater drain valves, shower and laundry mixing valves and fire protection sprinkler bodies
Electrical and utility industries
Fittings, switches, pole line hardware, connectors, breakers, fuse bodies, clamps, ferrules, cutouts and gas meter locks
Industrial
Locks, marine and boat hardware, fittings, connectors, pump and valve components and irrigation components
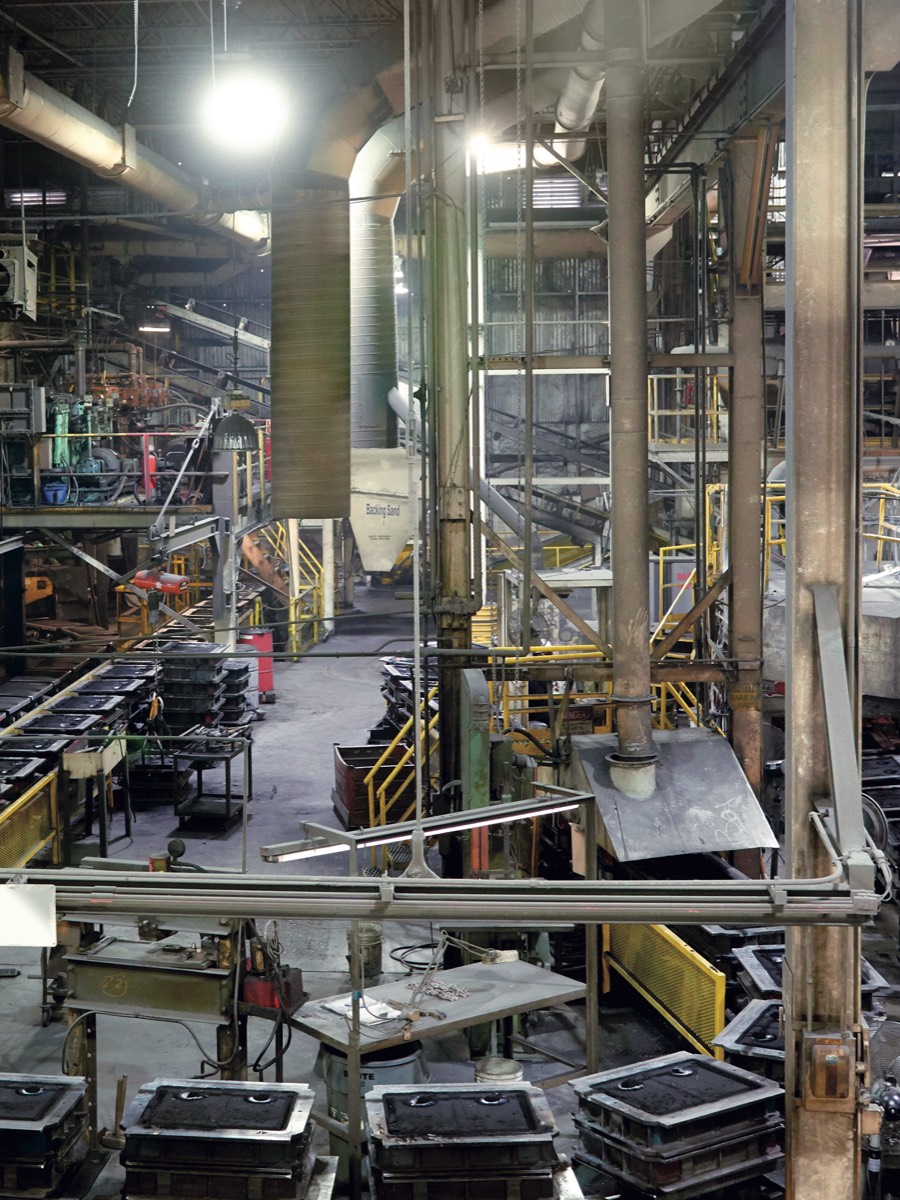
Investing in our future
Sloan has a rich heritage of innovation, and our Arkansas-based foundry is no different. We're committed to remaining at the forefront of the metal casting industry and have continually invested in the most modern equipment and software available.
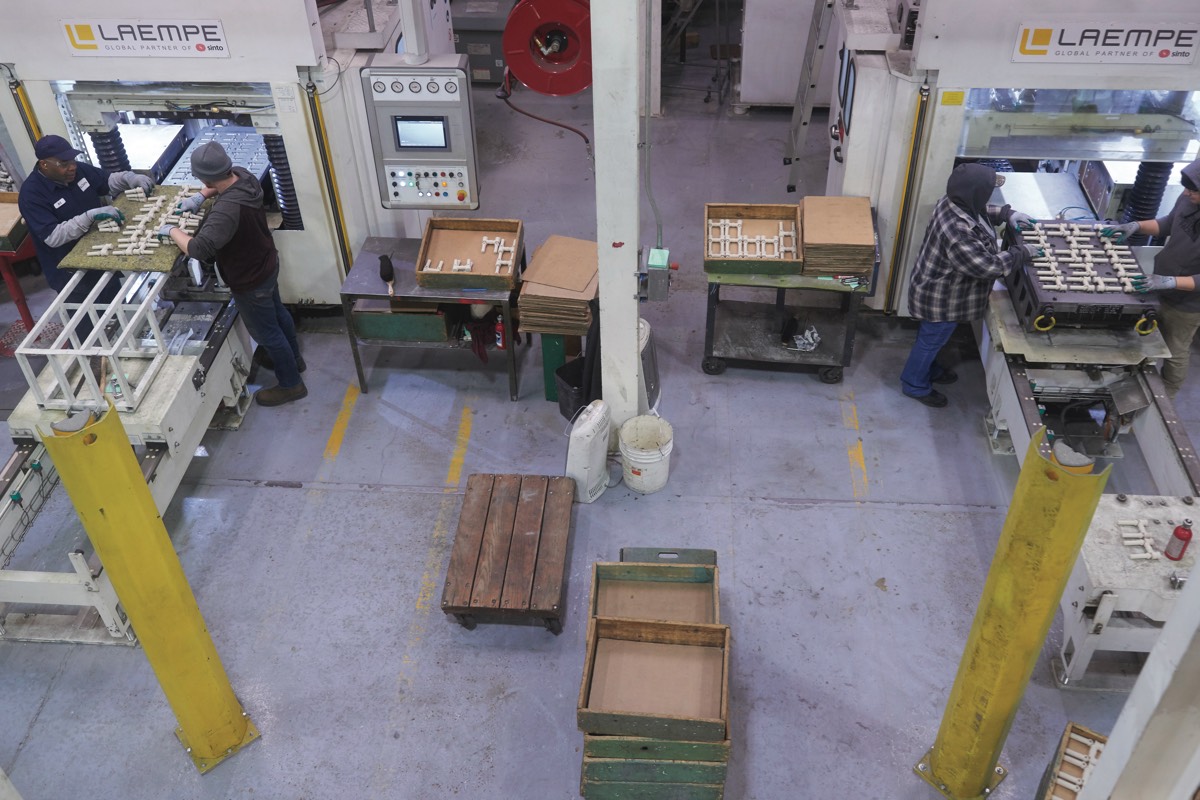
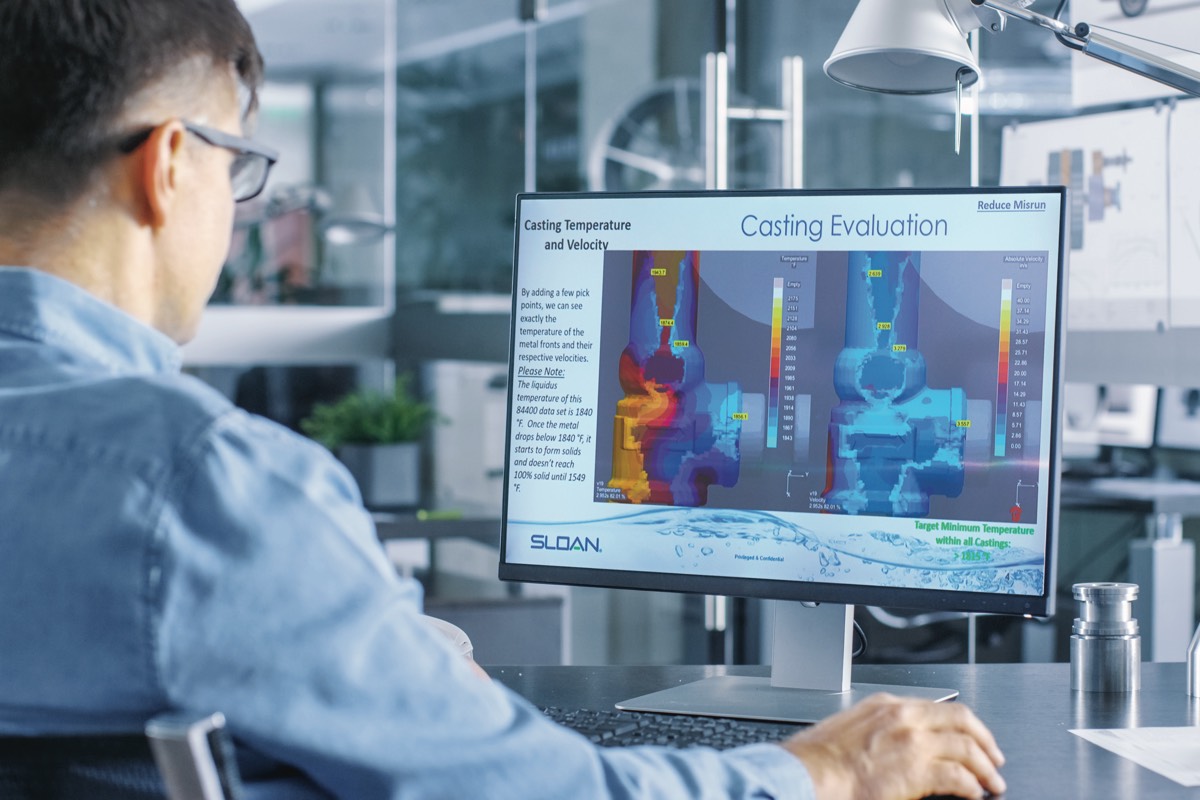
Advanced software
We use Magma modular software, which is a comprehensive and effective optimization tool for improving metal casting quality, optimizing process conditions and reducing production costs. This process ensures the structural integrity of your castings before production even starts.
Automatic core production
Sloan operates two LFB Series Laempe Core Shooter machines. Laempe machines offer the premium solution for semi-automatic and fully automatic core production, allowing for high performance product quality with around-the-clock continuous operation.
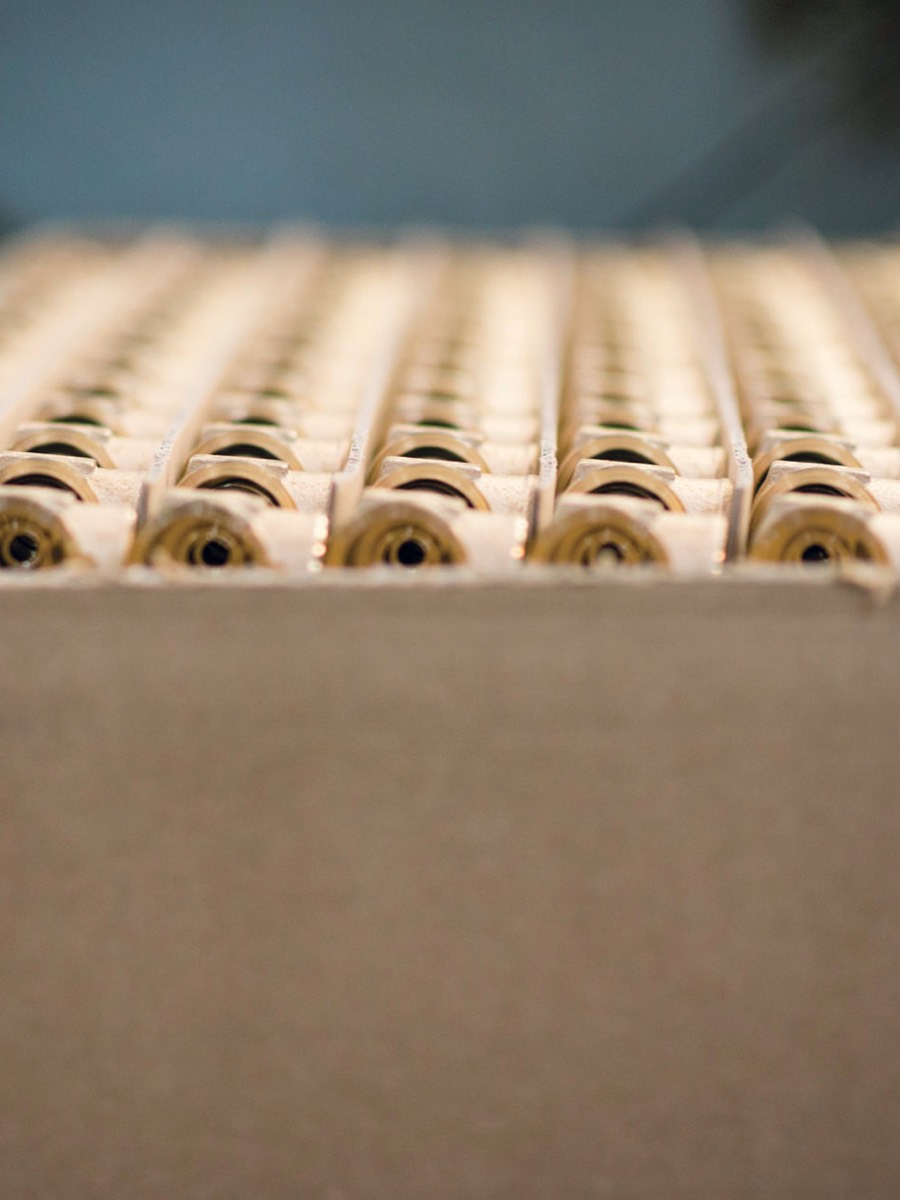
The proof is in the production
Sloan quality is stamped into everything we make. Our foundry has made the necessary adjustments to our sector-quality standards to become certified in the most recent ISO-9001-2015, ISO’s flagship standard for quality management systems.
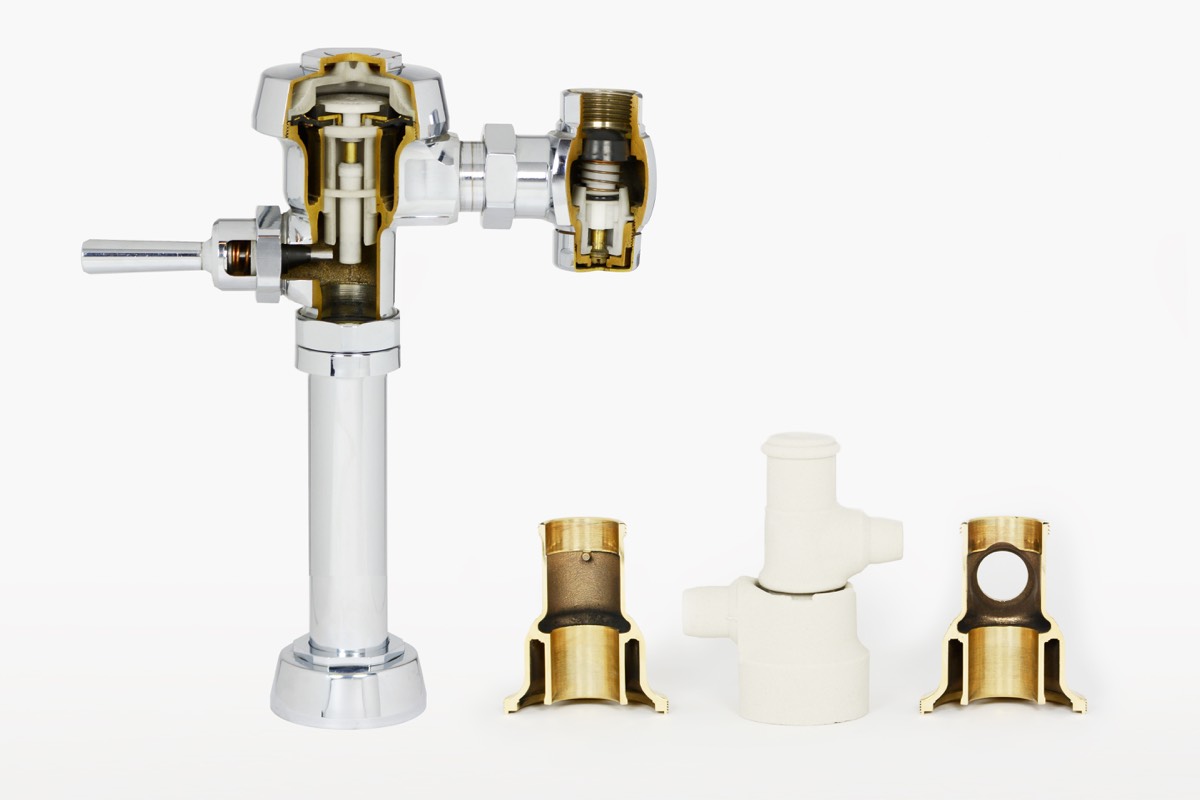
Quality assurance testing
At Sloan Foundry, we know how important it is to use quality castings. We use two types of testing, spectrographic metal control and tensile testing. By doing this, we can confidently deliver the exact strength and integrity for what is needed for your project.
The parts we produce are generally less than 10 pounds, with weights as low as .25 pounds, and typical annual production is at least 25,000 pounds of shipments per pattern.
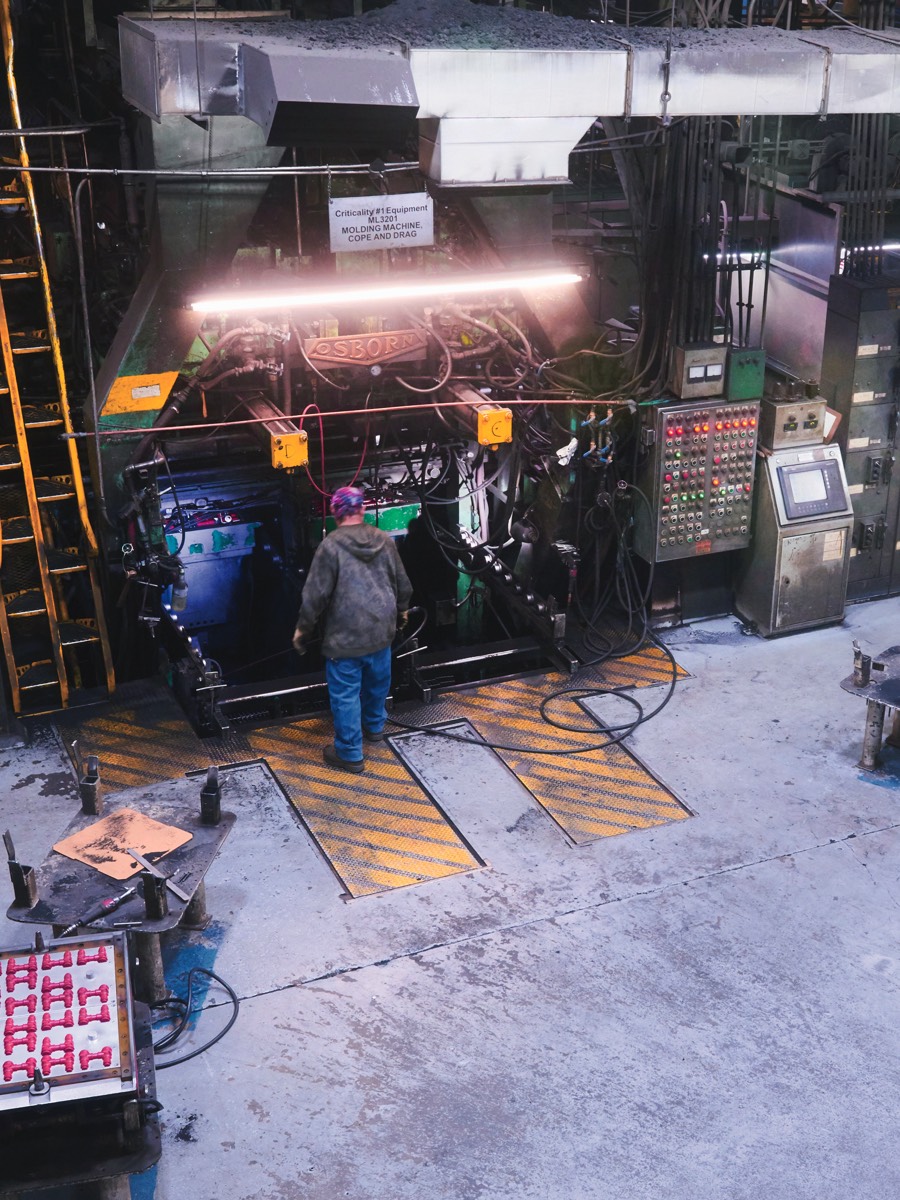
A world-class foundry on American soil
Our 160,000 square foot facility can provide castings, machining and even the assembly of products. We have a long-standing history with our customers and suppliers.
The success of our Arkansas foundry can be attributed to the experienced and skilled workforce we have had operating our machines for the past 40 years.
High production volume
Our high-production facility produces 60,000 pounds of CDA 84400 and CDA 83600 semi-red brass castings per day.
Tight flask molding
The heart of our production is the Osborn molding machine, which combines high production rates and matching core-setting capability. The tight flask system decreases the potential for a shift in the casting ensuring dimensionally accurate and consistent casting dimensions without sacrificing molding speed.
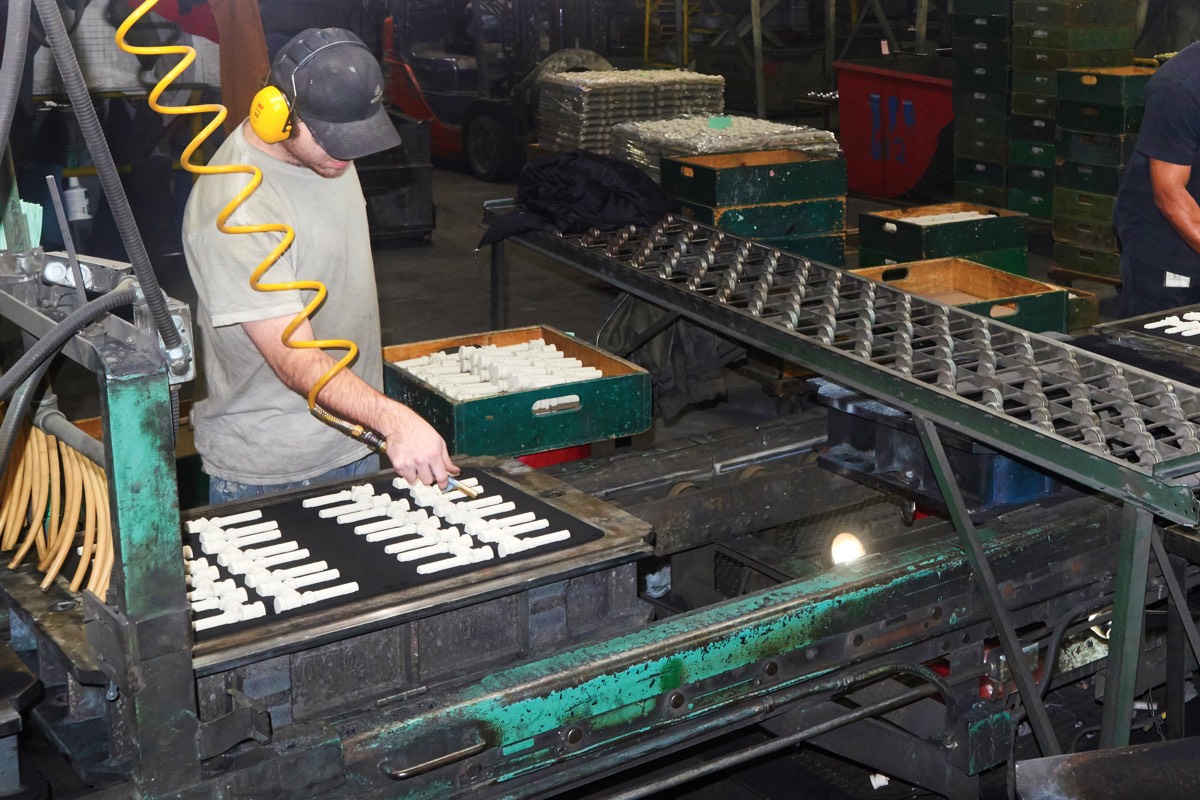
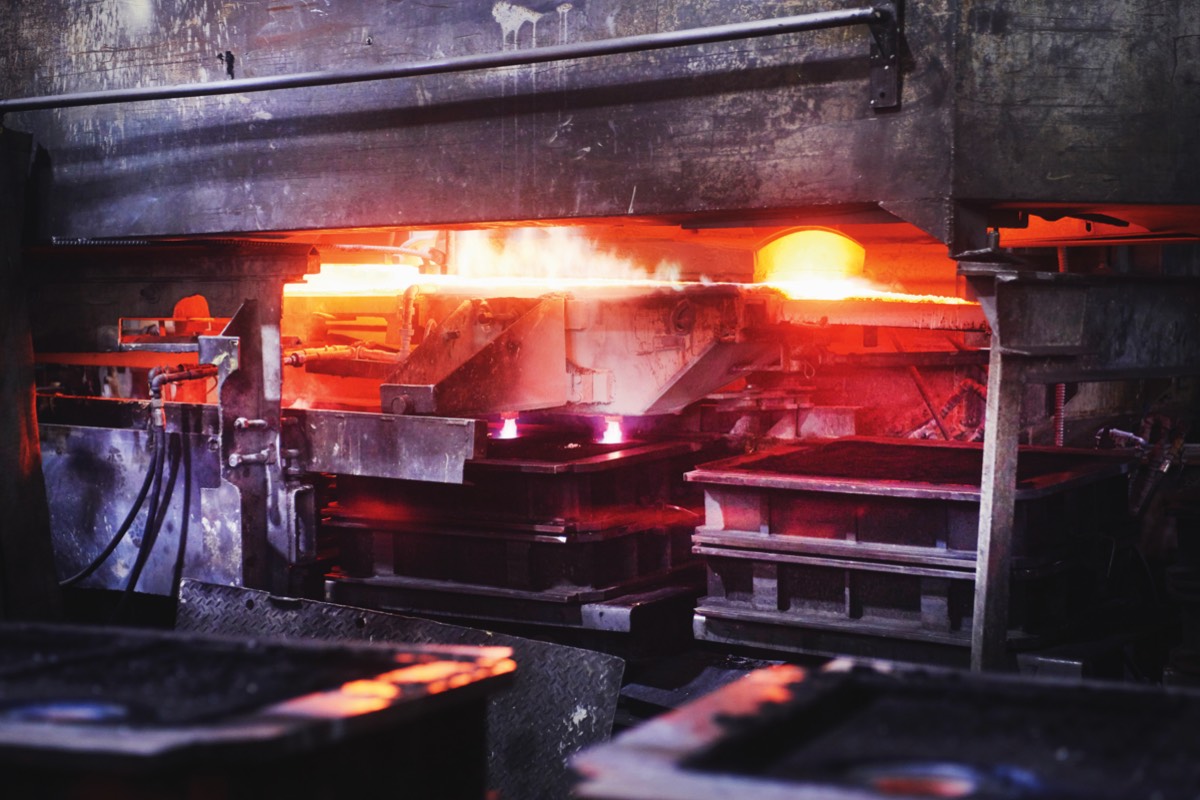
Foundry capabilities
Sloan is continually striving to produce quality castings that serve our customers specific needs. We are consistently developing new alloy options to meet the expanding interest in alternative casting materials.